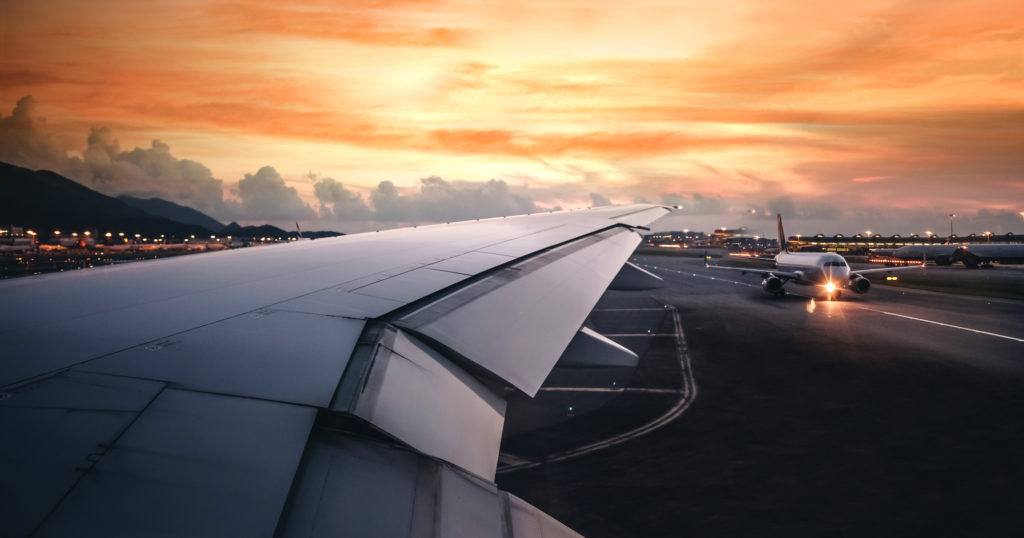
Airlines harbor a fear that dramatically increasing efficiency at their hubs would open landing slots, but that would put the hubbing airline in an elevated competitive position. More operations impacted by greater efficiency is going to have a greater c positive impact on the airline with the greater number of operations. And the costs of airline delays and congestion are huge.
GOOD NEWS! There is an independently validated (by the FAA, Embry-Riddle Aeronautical University, GE Aviation, and others) system solution available that can dramatically improve on-time performance, that can recapture 50% of the airline’s annual delay losses within months (Airline Business Based Flow Management (BBFM) White Paper 2018-02-06 ) and take the pressure off ATC.
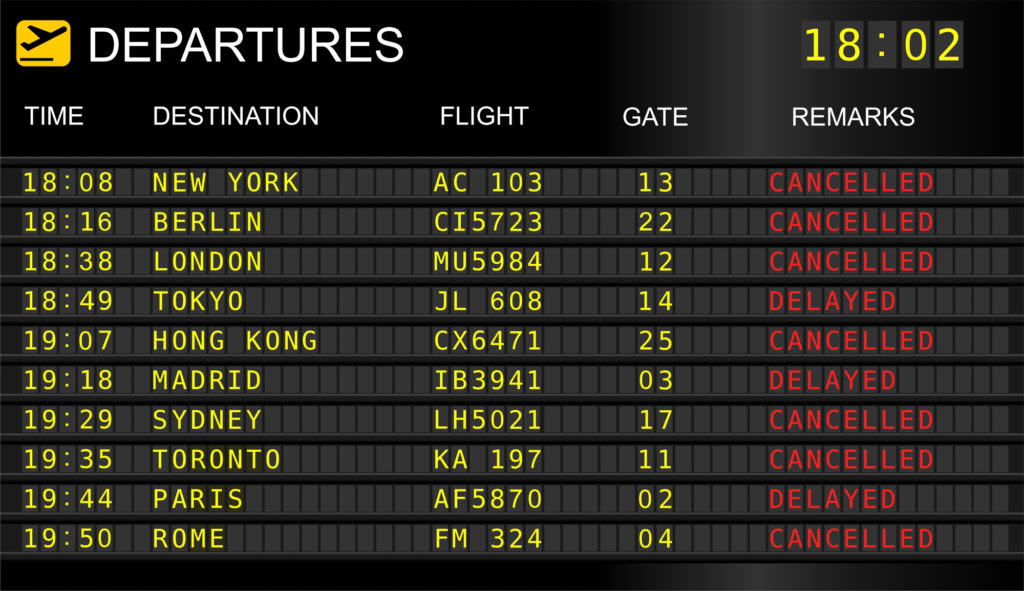
BAD NEWS! Unfortunately, airlines aren’t interested.
It can’t be fixed because . . .
Following are the invalid reasons that everyone erroneously cites why delays and congestion can’t be fixed.
1. Delays and congestion are ATC problems – Billions of dollars spent and decades have passed to revamp the ATC with the results always pushed further into the future with more billions of dollars attached. They’ve been given the shot over and over again. This alone should convince everyone that ATC will never fix delays/congestion. But there is an even bigger reason that ATC can’t efficiently fix delays – it’s not ATC’s job to make business decisions. For example, in a queue of ten tightly packed aircraft from the same airline approaching the hub, which aircraft should go first? Factors to consider include schedule, connections, gate availability, ramp assets, fuel, weather, diversion possibility, crew legality, maintenance, etc. Only the airline has the data to determine which is the “right” aircraft to move forward in the queue and which is the “right” aircraft to move backward in the queue, especially when balancing the goals of the 10 to 20 other aircraft trying to land around the same time. In fact, even with the exact same data, two different airlines would likely make different business decisions. How could ATC ever make an informed, efficient decision? It can’t.
2. There are too many variables – Yes, there are too many variables days or weeks prior to the flight. But, “day of”, two to five hours prior to landing, the situation has clarified dramatically. The data are there but not acted upon. Compiling the information the airline has readily available (FAA and Eurocontrol data showing aircraft position, altitude, speed, intent, aircraft position, weather data from the aircraft, Automatic Dependent Surveillance (ADS-B/C), ramp data from the airline, aircraft to ground digital data link [CPDLC], local radar data, accurate weather, etc.) reduces the variables to near zero from data available hours prior to landing. The next time you fly, consider the variables for your flight and you’ll find there are very few. Of course, we can’t know everything, like a blown tire closing a runway, but events like that are rare.
3. There are too many things the airline can’t control – Of course, airlines can’t control things like the weather, other airlines, an emergency, etc., but these impact less than 10% to 15% of an airline’s operation. That leaves upwards of 85% of the operation that an airline can control, yet doesn’t.
4. We need new technology to fix anything – ATC has been working on the “next great technological breakthrough” for decades, going through a host of alphabet-soup programs like the 1970s Microwave Landing System (MLS – cancelled), FAA’s 1980s Advanced Automation System to rebuild the ATC system (AAS – cancelled), FAA’s early 1990s downsized AAS rebuild proposal Initial Sector Suite System (ISSS – canceled), onboard navigation (RNAV), Global Positioning System (GPS), aircraft Traffic Alert and Collision Avoidance System (TCAS), Future Air Navigation System (FANS), CPDLC, ADS-B/C and now NextGen and Sesar, with little to no improvement. Today, all of the required technology is already in place in the aircraft and on the ground to dramatically reduce delays and congestion. Let’s use what we already have installed (and paid for) to develop new processes before spending more on new, untested and yet-to-be developed technology. We need a solution now and can’t keep waiting for highly complex programs like Artificial Intelligence, highly complex airspace structure, new technology, etc. to solve delays. This doesn’t mean stop the research, but it does mean build new, more efficient processes with the tools already in place. Currently this is not a focus for anyone.
5. Airports are full – Simply because you are on a 25-mile final doesn’t mean the airport is full. It does means is that the airport is overloaded at that time. Even Boise, which no one would call full, is overloaded when two aircraft want to land at the same time. On-time capacity exists even in the busiest airports, but it is forward in time. In fact, most of the congestion around an airport is actually the symptom of the unmanaged, highly random aircraft arrival flow.
So, what can, and should be done to prevent the overload in the first place? Consider two aircraft at the front of a tightly packed arrival queue of 30 aircraft. By identifying and accelerating the first two aircraft by moving them forward two minutes (accomplished hours prior to landing) the entire arrival queue moves forward. In other words, moving two aircraft forward at the front of a large arrival queue doesn’t just save two minutes, but saves two minutes for every aircraft in the queue behind the first two flights. The entire queue has moved forward. Dr. Clark of Georgia Tech labeled this “draft effect” that would drop 60 minutes of flight time (and delays) from this one arrival queue alone.
6. There is nothing you can do when a thunderstorm pops up at the airport – Thunderstorms really don’t just pop up out of nowhere. Thunderstorms need three ingredients; moisture, unstable air and lift, and usually associated with fronts. So, if a front is 60 miles northwest of the airport, moving southeast at 20 mph, it will impact the airport arrival fix (30 to 40 miles from landing) and the aircraft departure path in one hour and the airport in two to three hours. Despite this predictability, little to nothing is done until the thunderstorm directly impacts the operation.
So, the question remains – what can be done to mitigate this outcome? We all know the weather is coming, so the airline could reroute the aircraft to another arrival fix before ATC does it, speed up the inbounds to get them on the ground early, or slow down the aircraft to save fuel and avoid a divert. Or what about departure weather reroutes? What business person, knowing that west departures will be closed in 30 minutes, would taxi their $100 million capital asset (aircraft) from the gate and allow the government to manage it once in line for takeoff (ATC weather reroute)? Yet that is exactly what airlines do. The data exist to very accurately predict the arrival or departure constraints hours prior to departure, when airlines could easily act to prevent or lower the negative impact.
7. Airlines are doing everything possible to fix this – If this was accurate, airlines would not have a 30% daily defect rate (A0 around 70%, or less). Sadly, for passengers, shareholders and employees, airlines are comfortable with their current 1950s, “day of” production process, even when a much more efficient, independently validated, 21st century solution exists and has been field-tested for years.
8. NextGen/Sesar will fix airline delays – NextGen and Sesar, like other past ATC-centric programs that tried to fix delays, are just more of the same – high cost, extremely complex, technology-driven programs, with benefits always a decade and billions of tax dollars away. And what if they did succeed? The ultimate NextGen/Sesar goal is full ATC tactical control over the movement of the airline’s aircraft and customers, adding further inefficiencies. Consider a nor’easter under NextGen. ATC would manage the departure time, enroute speed, and most likely altitude and path of every east-bound flight. The communication and workload required by individual controllers, who, along with separating aircraft – their primary job, would be forced to sequence each of these aircraft from takeoff to landing. That doesn’t sound like a recipe for either efficiency or safety.
Variance
Variance is the root cause of most airline delays and the congestion we see in our airspace and airports. To better understand variance and its impact on arrival queuing, and therefore delays, we need to look at logistics and queueing. When variation increases, time in queue grows exponentially. Driving out variation is something only the individual airlines can efficiently achieve because only the airline has all of the business data to understand the “day of” variance in the first place (schedule, fuel, connections, gate availability, crew legality, maintenance requirements, deicing, ramp assets, etc.). Airlines could. Airlines should. Airlines don’t.
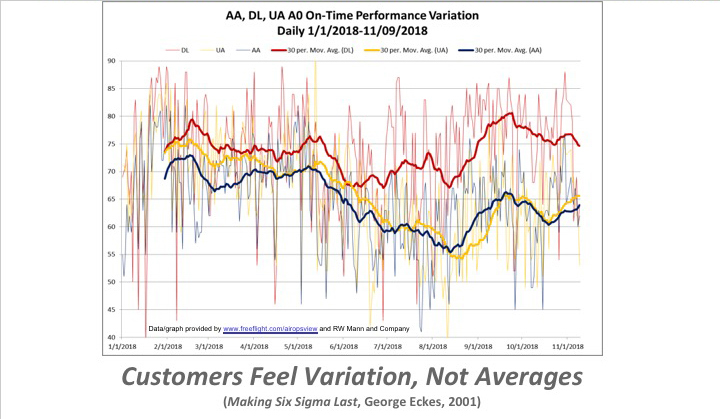
Unforced Errors
Given the linear nature of airline operations (e.g. cleaning must be done before boarding, the repair must be done before the paperwork is completed, the departing aircraft must leave the gate before the next aircraft can park, etc.) any error, while small by itself, has a huge negative impact on the efficiency of the overall operation. How many times has an aircraft pulled up to its gate and had to wait for someone to guide the aircraft to parking or for a jetway driver? How many times has the aircraft sat at the gate for ten minutes waiting on the “final paperwork?” How many times did your flight land without a gate, but there were gates open, just not yours? These are all internal airline process errors which should simply never happen – not once, not ever.
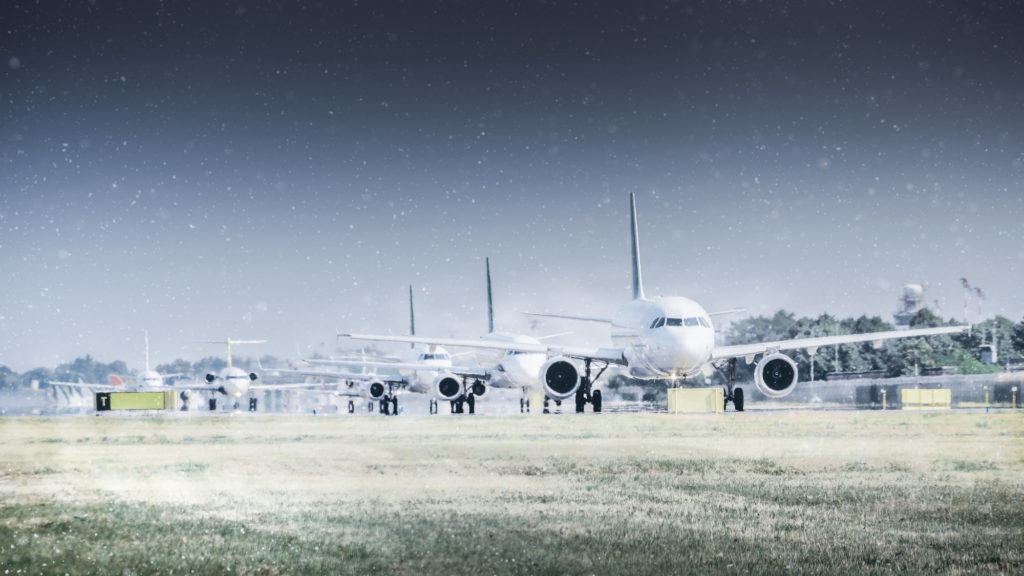
Consider that to move an airplane from gate to gate requires about 15 vital processes, Now if each process in the task averages a 97% success rate (complete and on time), it sounds pretty good. But given the compounding nature of a linear process, 15 processes at a 97% success rate will only achieve a 63.3% success rate for the overall task (.97 to the 15th power). For the same 15-step linear task to achieve an 86% success rate requires a 99% rate of success for all of the processes. Failure of each of the individual process can be harmful by themselves. For example, in what operational model does it make sense to shut down (park) a $100 million production facility (aircraft) 50’ from the gate for the want of a $30/hr. employee? Outside of our industry, it wouldn’t happen.
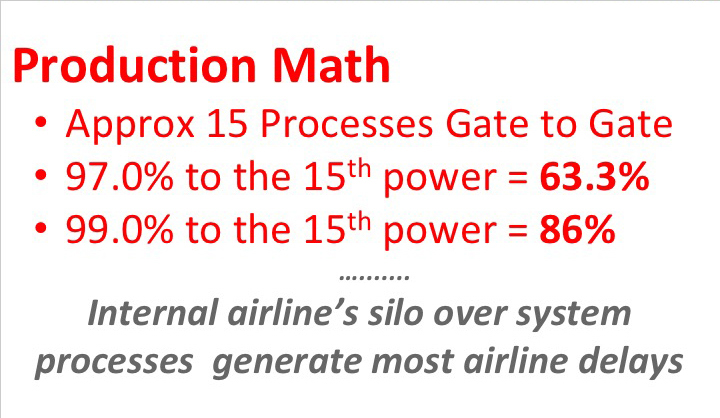
The Costs
The analysis is quite clear – the airline industry’s poor “day of” operational quality (30% daily A0 defect rate) costs billions annually. ATC, airports and weather unfairly get the lion’s share of the blame and governments spend billions of tax dollars in unsuccessful efforts to find a fix.
In a 2019 analysis of airline delay costs in a recent Forbes.com article, The Fastest Airlines in the US , they looked at every US city pair and compared the delay performance of the individual flights (8.1 million of them). The research concluded that in 2018, the total costs of delays to airlines, travelers and the economy was $88 billion. The cost of delays and inefficiency is HUGE – huge for everyone; airlines, passengers, shareholders, ATC, airports, governments, taxpayers, crews, employees, the economy and the environment.
Bottom line is that the current locally based, ATC/controller/government centric aircraft sequencing solution has never, and will never make airspace, airports and/or airlines efficient and costs will continue to rise.
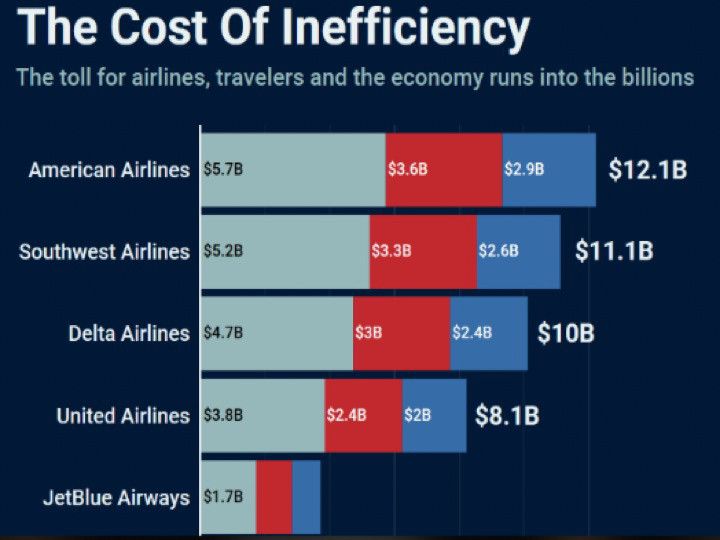
The Solution
The culprit is variance and unforced errors that only the airlines could fix, airlines should fix, but airlines don’t fix. As a first step, airlines must manage their aircraft in real time, hours prior to landing, to precondition the aircraft arrival flow before it reaches the airport
– i.e., don’t overload the box.
Within months, airlines could tactically control their aircraft to deliver a more rational, efficient, stable flow to ATC near the airport, eliminating many of the problems we accept as normal (delays, congestion, ATC structure, etc.). In other words, if instead of forcing ATC to play 52-card pickup with highly variant arrival flows, airlines could reduce delays, congestion and make ATC’s job much simpler by tactically managing the arrival queue to deal ATC a much better hand to start with.
Consider the example of a single airport, with four arrival fixes. If this airport can handle 60 arrivals per hour, 1 per minute, and the airlines randomly throw 45 arrivals at the airport in 30 minutes, the airport is overloaded. ATC very predictably sequences and queues up the arrivals backwards in time, first-come first-served, on a 20 to 30 mile final. Conversely, with the data available today, the airline could easily predict this negative outcome and act to prevent it hours prior to landing. The reactionary response in the scenario is defect correction. Our goal is defect prevention.
And there is a readily available, low cost solution — Business Based Flow Management (BBFM).
BBFM is the only real-time, independently validated, system optimized, “day-of”, flight arrival queue management solution, based on the airline’s defined business rules and airport demand/capacity, which can be coordinated with ATC and the airport in real time. BBFM has been independently validated to improve on-time performance, improve product quality, lower costs, lower CO2 emissions and generate highly accurate ETAs worldwide. It uses a stepped implementation and current systems and technology.
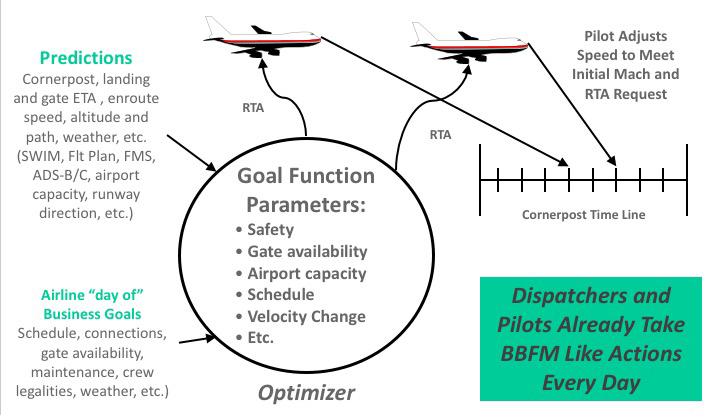
BBFM does this by identifying every arrival to the airport, tracks its position, speed and altitude in real-time, as well as the flight plan path and real-time winds to accurately predict the arrival fix, runway and gate ETAs. BBFM then evaluates the value of the outcome of the predicted gate arrival time for each aircraft at that airport from a system perspective (taking into account; schedule, gate availability, ramp, fuel, capacity, demand, maintenance, crew legality, etc.) for all of the airline’s arrivals. Within seconds, BBFM evaluates literally thousands of iterations of speeding up some aircraft, slowing down others to find a better “system” outcome. BBFM then automatically sends each pilot a Required Time of Arrival (RTA) via ACARS , two to three hours prior to landing. The time changes average two to four minutes. The pilot adjusts speed for the arrival fix at the specified RTA. Typically, the speed change is 10 to 20 mph, well under the speed change that necessitates notifying ATC (10 mph or 5% of filed True Airspeed, whichever is higher).
Another unique benefit of the airline-centric BBFM solution is that it easily crosses sovereign airspace (FIR) and ATC sector boundaries. This is an absolute necessity for any successful “day of” queue management solution and a huge political and technical limitation inherent in any current and proposed ATC centric program.
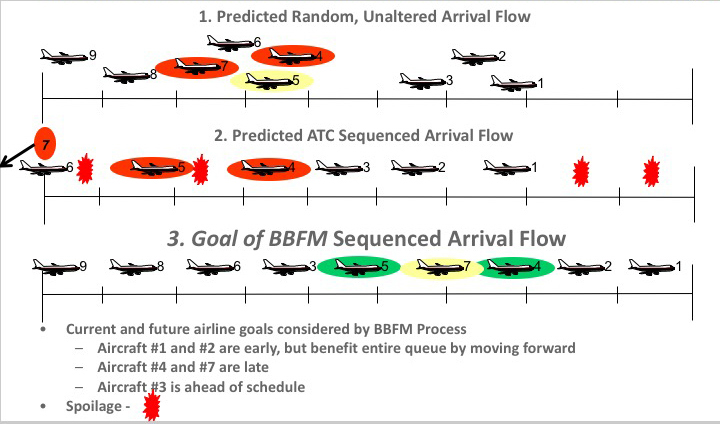
This explanation, in the interest of time is space, is simplistic and likely has you formulating lots of questions and what-if scenarios. Research and real-world use have addressed every question. Over years of use by major airlines at major hubs has answered them all. But, what needs to be our focus is that the industry and governments have long been focusing on the wrong problem. Your peers (pilots) have arrived at a solution, tested it and had it independently evaluated. Where we have landed is upon a solution that employs the predictive analytics in the same way we have come to rely on our traffic-enabled GPS systems in our cars (e.g. WAYZ). The system employs defect prevention not defect correction. (Let’s prevent the problem, not scramble to correct it.)
If your airline were to invest in this system and save hundreds of millions of dollars, it might be a little easier for the unions to negotiate. Wouldn’t we rather have our representatives argue for increased profits first then try to get us a slice of that? Start the conversation. It’s coming to a future near you and the sooner it arrives the better for the lot of us – as pilots, cogs in the wheels of our economy, even as inhabitants of Planet Earth.
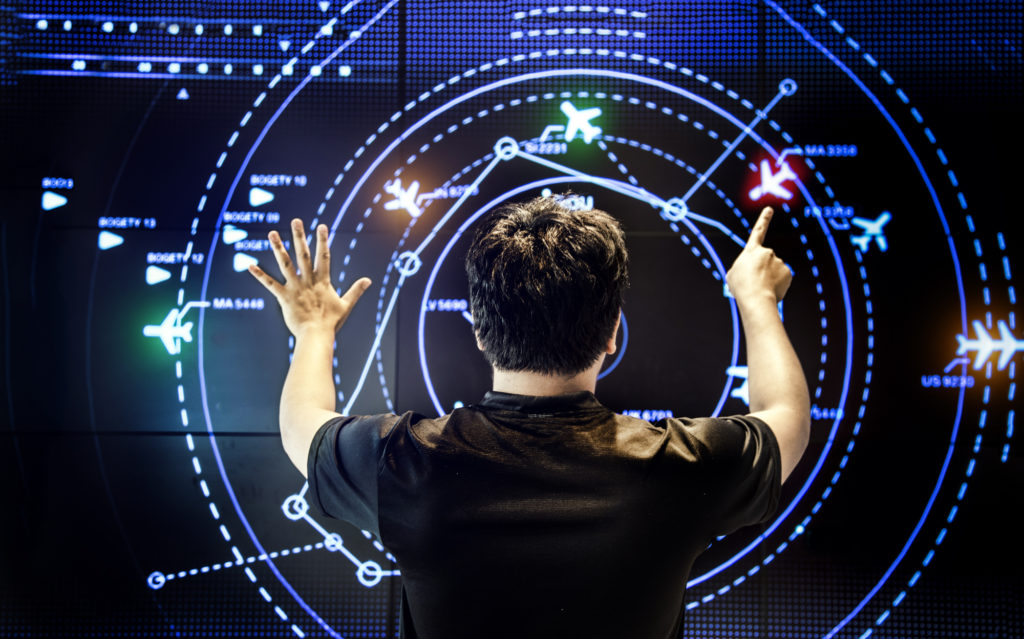
___________________
Additional articles outlining why the Operational Excellence solution (85% A0, <3% day to day A0 Standard Deviation, 8- to 10-minute scheduled block/gate time reduction per flight), driven by Business Based Flow Management (BBFM), is the path forward to make airlines dramatically better and more profitable. Like Toyota did in the 1980s for the auto industry, all it takes is one airline and/or ANSP to lead the way.
Air Traffic Control Is Not The Real Cause Of Airline Delays (Forbes.com, 2017-03-23)
Congestion – Who’s to Blame (FAAMA Managing the Skies, Summer-Fall 2018)
Why Airlines Make Flight Longer on Purpose (BBC Capital Smart Travel, 2019-04-09)
Not Working! (ATCA Tech Symposium, Atlantic City, 2018-05-16)
Parked Planes Cost Airlines Billions (Forbes.com, 2017-08-15)
Attila Arrives (Aviation Week, 2013-01)
Airline Business Based Flor Management
The Fastest Airlines in the U.S.
For the record, my partner and I developed Business Based Flow Management (BBFM), previously branded as Attila™, and I have a vested interested in its success.
Aircraft Communications Addressing and Reporting System – Aircraft to ground data link communication process in place since the 1980s.